Products >> Titanium >>
Sewage treatment titanium anodes
- Product No.:2023911131015
- Material Grade:titanium alloy
Titanium anodes are electrodes made of titanium or its derivative alloys that are utilized in numerous electrochemical processes, including electroplating, electrolysis, water treatment and cathodic protection. Titanium has long been chosen due to its resistance to corrosion, high conductivity and long lifespan - qualities that make it the go-to material.
Processing titanium anodes involves several steps, such as:
Material Selection: Selecting an ideal titanium grade and alloy composition that best meets the unique application needs for an application, including electrolyte composition, current density requirements and operating environment requirements is of utmost importance when making material selection decisions.
Anode design involves selecting and creating an anode of appropriate shape, size and configuration that meets specific application and performance goals - this may involve mesh, plate, rod ribbons or any number of other specialized forms as needed for optimal anode performance.
Fabrication: Utilizing techniques such as laser cutting, CNC machining or stamping to cut, shape, and form titanium material into desired anode shapes is known as fabrication.
Surface Treatment: Enhancing an anode's performance and durability through surface treatments such as sandblasting, pickling, acid etching or plating it with precious metal oxides such as ruthenium, platinum or iridium oxide coating is one way of increasing performance and durability. These processes could include techniques like sandblasting, pickling or acid etching as well as coating it with precious metal oxides such as ruthenium, platinum or iridium oxide coatings.
Electrical Connection: Securing the titanium anode with power sources or electrolyte via suitable connectors or coatings will enable for its connectivity with electrolytic solutions or sources.
Quality Control: Undergoing rigorous quality control tests is key to making sure anodes comply with specifications in terms of corrosion resistance, electrical conductivity and dimensional accuracy.
Testing and Certification: Before they're certified as released for use, anodes undergo thorough tests for performance such as polarization, current efficiency and lifespan evaluations to ensure optimal functionality and lifespan.
Titanium anodes offer several distinct advantages over their rival materials, including long service lives, lower maintenance requirements and the resistance of highly corrosive environments. As a result, these anodes are increasingly being utilized by industries that rely heavily on electrochemical processes, including electroplating, water treatment, chemical processing and metal electrowinning for various purposes.
Titanium anodes require multiple steps during production. They include:
Titanium anodes are electrodes made from titanium or its derivative alloys used for various electrochemical applications, including electroplating, electrolysis, water treatment and cathodic protection. Titanium has become popular as an anode material due to its excellent corrosion resistance, high conductivity and long lifespan - all qualities essential in any anode material.
Titanium anodes require multiple steps during production. They include:
Materials Selection: Selecting an ideal titanium grade and alloy composition that best meets your application specifications such as electrolyte type, current density requirements and operating environment is of key importance in meeting all application demands.
Anode Design: Crafting the shape, size, and configuration of an anode specifically tailored for its intended application to maximize efficiency of performance. This could involve designing mesh screens, plates, rods, ribbons or any other specialty forms into an anode structure.
Fabrication: Titanium material must first be cut, shaped and formed into its desired anode shape using methods like laser cutting, CNC machining or stamping to achieve this aim.
Surface Treatment: Enhancing anode surface performance and durability through treatments like sandblasting, pickling, acid etching or coating with precious metal oxides such as ruthenium, platinum or iridium can enhance its performance and lifespan. These processes might involve techniques like sandblasting, pickling and acid etching as well as coating it with precious metal oxides like ruthenium platinum and iridium oxide.
Electrical Connection: Establishing an effective way for connecting the titanium anode to its power source or electrolyte with appropriate connectors or coatings that conduct electricity.
Quality control: Conducting stringent quality control tests to verify that anodes meet specifications regarding corrosion resistance, electrical conductivity and dimensional accuracy.
Testing and Certification: Testing anodes for their performance such as polarization, current efficiency and lifespan before they are certified for use is crucial to their certification and release for use.
Titanium anodes provide several distinct advantages over their competitors, including longer service lives, lower maintenance requirements, increased stability and resistance to highly corrosive environments. They're widely utilized by industries like electroplating, water treatment, chemical processing and metal electrowinning relying heavily on electrochemical processes for various purposes.
Previous Product:titanium pipe and fittings
Next Product:Titanium tube sheets for heat exchangers
Contact Us
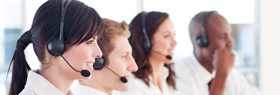
Name: Mr. Ren
Tel: +86-18292471213
E-mail: info(at)intemetal.com
Add: Middle Section Baotai Road, Weibin District, 721013, Baoji, Shaanxi Province, China