Products >> Molybdenum >>
High temperature resistantant molybdenum crucible
- Product No.:Mo crucible
- Material Grade:99% purity molybdenum
Molybenum crucibles physical properties:
1. High temperature resistant: molybdenum crucibles can be mainly divided into sintered molding, press molding, spinning molding, turning forming and welding forming. It is mainly made from turning forming. Molybdenum crucible for vacuum coating refines from Mo-1 powder. Its appropriate working temperature should be within the range from 1100℃ to 1700℃.The melting point of molybdenum crucible for vacuum coating is as high as 2610℃.
2. High purity: Hengze Industry Co., Ltd. is proud to offer high purity molybdenum products to meet the stringent requirements of various industries. Or high purity molybdenum is produced using advanced manufacturing processes and strict quality control measures, ensuring exceptional purity levels. High purity molybdenum is widely used in applications that demand exceptional heat resistance, electrical conductivity, and mechanical strength. Whether you require high purity molybdenum rods, sheets, or other customized products, you can rely on Hengze Industry Co., Ltd. for reliable and top-quality solutions. 99% high purity molybdenum crucible mill test report sample as following:
Mill Test Report
Item Name:Molybdenum Crucible |
|
||||
Heat No:2023003100 |
|
||||
|
|
||||
Chemical Composition(%) |
|||||
Si<0.001 |
Cu<0.0003 |
Bi<0.001 |
|||
Al<0.0015 |
Cd<0.001 |
Se<0.001 |
|||
Fe<0.0005 |
Ca<0.001 |
W<0.015 |
|||
P<0.001 |
Pb<0.001 |
Ni<0.0007 |
|||
Mg<0.0001 |
N<0.002 |
K<0.003 |
|||
C<0.002 |
Cr<0.002 |
S<0.002 |
|||
Mn<0.0005 |
|
|
|||
Remark |
Mo≥99.95% |
|
|||
Inspector: 01 |
Date: March, 2023 |
||||
Mechanical and chemical properties:
Molybdenum distinguishes itself with those unique properties: high melting point, high creep resistance and low thermal expansion.
The properties of the pure molybdenum could also be improved by alloying. According to the application environments and the operating temperatures, we offer the best molybdenum alloy for our customers.
Molybdenum has extremely good resistance to corrosion by numerous acids, liquid metals and molten glass, provided oxidizing agents
are not present. Molybdenum is relatively inert in hydrogen, ammonia, and nitrogen up to about 1100°C.
What is the production process of molybdenum crucible?
The production process of molybdenum crucible involves several key steps. First, molybdenum ore is mined and processed to extract the molybdenum metal. The extracted molybdenum is then purified through a series of chemical and metallurgical processes to remove impurities and achieve the desired purity level.
Once the purified molybdenum is obtained, it is then shaped into the desired crucible form using techniques such as pressing, sintering, and machining. These processes involve shaping the molybdenum into a crucible mold and then subjecting it to high temperatures to achieve the final shape and properties required for its intended use. Finally, the finished molybdenum crucibles undergo quality control checks to ensure they meet the required specifications before being made available for industrial applications.
Overall, the production process of molybdenum crucible involves mining, extraction, purification, shaping, and quality control to produce high-quality crucibles suitable for various high-temperature applications in industries such as metallurgy, glass manufacturing, and semiconductor production.
Molybdenum is widely used to produce crucibles and other parts for Sapphire crystal growth and rare-earth melting with its high
temperature resistance, low pollution and other good characteristics.
1.Molybdenum crucibles are mainly used in metallurgy industry, mechanism process industry and rare earth smelting industry;
2.They are more frequently used in crystalloid materials and other burgeoning high-tech industries;
3.The crucibles should be used in vacuum or deoxidize atmosphere and the highest using temperature should be no more than 2000ºC.
Molybdenum crucibles are widely used in a variety of industries, including:
- Metallurgy: Molybdenum crucibles are used to melt and cast a variety of metals, including aluminum, copper, gold, silver, and platinum.
- Rare earth industry: Molybdenum crucibles are used to smelt and refine rare earth metals, such as neodymium, dysprosium, and gadolinium.
- Monocrystalline silicon: Molybdenum crucibles are used to grow monocrystalline silicon boules, which are used in the manufacture of solar cells and semiconductors.
- Solar energy: Molybdenum crucibles are used to produce solar-grade silicon and other materials used in solar cells.
- Artificial crystal: Molybdenum crucibles are used to grow artificial crystals, such as sapphire and quartz.
- Mechanical processing: Molybdenum crucibles are used to sinter and anneal metal parts.
- Molybdenum crucibles are chosen for these applications because they offer a number of advantages over other materials, including:
- High melting point: Molybdenum has a melting point of 2623°C, which makes it suitable for melting a wide range of metals and other materials.
- Excellent corrosion resistance: Molybdenum is resistant to corrosion by most acids and alkalis, making it suitable for use in a variety of chemical environments.
- Good thermal conductivity: Molybdenum has good thermal conductivity, which helps to ensure even heating of the material being processed.
- High strength: Molybdenum is a high-strength material, which makes it resistant to cracking and deformation.
Molybdenum crucibles are typically used in high-temperature furnaces. They are often used in conjunction with other refractory materials, such as graphite or alumina, to protect the crucible from damage.
Here are some specific examples of molybdenum crucible applications:
- Melting and casting aluminum alloys for use in the automotive and aerospace industries
- Smelting and refining rare earth metals for use in electronics and magnets
- Growing monocrystalline silicon boules for use in solar cells and semiconductors
- Producing solar-grade silicon for use in solar cells
- Growing artificial sapphire crystals for use in LED substrates and other optical applications
- Sintering and annealing metal parts for use in a variety of industries
What are the mostly used sizes of molybdenum crucibles?
Molybdenum crucibles are typically available in the following general sizes:
- Volume: 5ml - 100ml
- Diameter: 10mm - 70mm
- Height: 10mm - 100mm
These are general sizes, and specific dimensions may vary depending on the manufacturer and the intended application. For example, crucibles for melting metals may need to be larger and more robust than crucibles for chemical analysis.
Here are some specific examples of molybdenum crucible sizes:
- 5ml crucible: 10mm diameter x 10mm height
- 10ml crucible: 15mm diameter x 15mm height
- 25ml crucible: 20mm diameter x 20mm height
- 50ml crucible: 25mm diameter x 25mm height
- 100ml crucible: 30mm diameter x 30mm height
Frequently asked questions and answers:
1. What are molybdenum crucibles?
Molybdenum crucibles are vessels made from molybdenum, a refractory metal known for its high temperature resistance and excellent corrosion resistance. These crucibles are used in high-temperature applications such as melting and casting metals, sintering, and heat treatment processes.
2. What are the benefits of using molybdenum crucibles?
Molybdenum crucibles offer several advantages, including:
High temperature resistance: Molybdenum can withstand extremely high temperatures, making it suitable for use in applications where other materials would fail.
Corrosion resistance: Molybdenum resists attack by most acids and aggressive chemical environments.
Excellent thermal conductivity: Molybdenum efficiently transfers heat, allowing for uniform heating and cooling of materials within the crucible.
High mechanical strength: Molybdenum crucibles have good mechanical stability, ensuring durability and longevity.
3. What industries use molybdenum crucibles?
Molybdenum crucibles are commonly used in industries such as:
Metallurgy: Crucibles are utilized in the production and exploration of various metals and alloys, including steel, superalloys, and rare earth metals.
Electronics: Molybdenum crucibles are employed in the manufacturing of semiconductors, LED lights, and other electronic components.
Materials research: Crucibles play a crucial role in experimental studies, phase transitions, and sample preparations in research laboratories.
4. How should molybdenum crucibles be handled and maintained?
To ensure the longevity and optimal performance of molybdenum crucibles:
5. Handle them with care to avoid impact or shock.
Clean them regularly using mild cleaning agents and avoid abrasive materials that can damage the surface.
Avoid exposure to corrosive substances that could compromise the crucible's integrity.
Store them in a dry, clean place away from moisture and contaminants.
Follow proper heating and cooling procedures to prevent thermal shock.
6. Can molybdenum crucibles be customized?
Yes, molybdenum crucibles can be customized to meet specific requirements. Crucibles can be manufactured in various shapes and sizes, including cylindrical, conical, or rectangular forms, depending on the intended application. Customized features such as lids, handles, or special coatings can also be added as per the customer's needs.
Contact Us
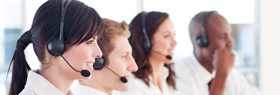
Name: Mr. Ren
Tel: +86-18292471213
E-mail: info(at)intemetal.com
Add: Middle Section Baotai Road, Weibin District, 721013, Baoji, Shaanxi Province, China